Industrial manufacturing is a precision-driven industry where maintaining strict control over every aspect of the production process is essential for ensuring quality, yield and overall safety of the facility and operators. One of the critical components that support this level of control is the HOT-TAP Valve Retractable Assembly. These assemblies allow for the insertion and removal of sensors into process tanks or pipelines without interrupting operations, making them invaluable in pharmaceutical environments where continuous monitoring and process integrity are crucial.
Key Uses of HOT-TAP Valve Retractable Assemblies in Industrial Manufacturing
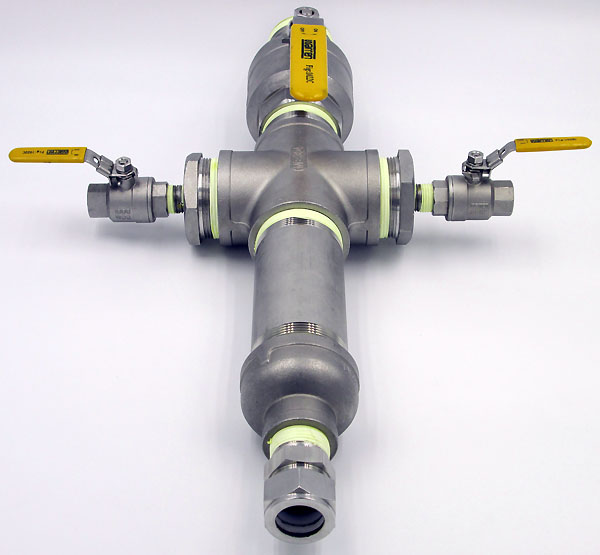
- Real-Time Monitoring of Critical Parameters In industrial manufacturing, monitoring parameters such as pH, ORP, and temperature is essential to ensure that chemical reactions and biological processes occur within the specified ranges. HOT-TAP Valve Retractable Assemblies allow sensors to be inserted directly into the process stream, providing real-time data without the need to halt production.
- pH Monitoring: Accurate pH control is vital for the stability of many industrial products. HOT-TAP assemblies enable the continuous measurement of pH levels in process lines, tanks, and mixing vessels ensuring that the environment remains within the required parameters.
- ORP Monitoring: Oxidation-Reduction Potential (ORP) is a key indicator of the oxidation state of a chemical process. By using HOT-TAP assemblies, ORP sensors can be inserted into the process, allowing for real-time adjustments to be made to maintain the desired redox conditions.
- Ensuring Sterility and Process Integrity Sterility is a non-negotiable requirement in certain food and beverage manufacturing. The ability to insert and retract sensors without exposing the process to contamination is a significant advantage provided by HOT-TAP Valve Retractable Assemblies. In particular the pH and ORP sensors employed must be able to withstand exposure to the chemical clean in place (CIP) process as well as periods of prolonged dryness in between batches as well as unexpected shutdowns.
- Sensor Maintenance: Regular maintenance and calibration of sensors are necessary to ensure accurate readings. HOT-TAP assemblies allow for the easy removal and replacement of sensors without stopping the process or compromising sterility, ensuring that the production environment remains uncontaminated.
- Process Validation: During process validation, sensors may need to be added or adjusted to ensure the process is operating within validated parameters. HOT-TAP assemblies facilitate these adjustments without disrupting the validated state of the process.
- Supporting Continuous Manufacturing Continuous manufacturing is becoming increasingly common in the industry due to its efficiency and ability to produce high-quality products with less variability. HOT-TAP Valve Retractable Assemblies are particularly well-suited to continuous manufacturing environments, where uninterrupted monitoring and control are essential.
- In-Line Monitoring: Continuous processes require in-line monitoring to ensure that every stage of production meets quality standards. HOT-TAP assemblies enable the placement of sensors directly in the production line, providing real-time data that can be used to make immediate adjustments.
- Reduced Downtime: The ability to maintain, replace, or calibrate sensors without shutting down the process reduces downtime and increases the overall efficiency of continuous manufacturing operations.
- Enhancing Process Safety and Compliance The industrial manufacturing processes are subject to stringent regulatory requirements that mandate the monitoring and documentation of critical process parameters. HOT-TAP Valve Retractable Assemblies play a crucial role in ensuring that these requirements are met by providing reliable, real-time data that supports process safety and compliance.
- Regulatory Compliance: HOT-TAP assemblies enable continuous monitoring of parameters that are critical for regulatory compliance, such as pH and ORP. This helps manufacturers maintain detailed records that demonstrate adherence to industry standards.
- Safety Assurance: By allowing for the safe insertion and removal of sensors, HOT-TAP assemblies minimize the risk of accidents or contamination that could compromise product quality.
- Applications in Biopharmaceuticals The production of biopharmaceuticals, including monoclonal antibodies, vaccines, and gene therapies, requires precise control of environmental conditions to ensure the viability of biological products. HOT-TAP Valve Retractable Assemblies are instrumental in maintaining these conditions throughout the production process.
- Bioreactor Monitoring: Bioreactors are at the heart of biopharmaceutical production, and maintaining the correct pH, temperature, and dissolved oxygen levels is critical. HOT-TAP assemblies allow sensors to be placed directly in the bioreactor for continuous monitoring, ensuring that the culture environment is optimal for cell growth and product yield.
- Aseptic Processing: In aseptic processing, the ability to monitor and control process parameters without introducing contaminants is vital. HOT-TAP assemblies provide a way to do this, ensuring that the aseptic conditions required for sterile product manufacturing are maintained.
Conclusion
HOT-TAP Valve Retractable Assemblies are indispensable tools in industrial manufacturing, where precision, reliability, and continuous monitoring are of utmost importance. Their ability to provide real-time data, support continuous manufacturing, and ensure process safety and compliance makes them a critical component in the production of high-quality industrial and pharmaceutical products. As the industry continues to evolve, the use of HOT-TAP assemblies will remain a cornerstone of efficient, safe, and compliant manufacturing practices.