Conductivity measurement is a critical parameter in many industrial processes. It is used to assess the ability of a solution to conduct electricity, which is directly related to the concentration of ions in the solution. Conductivity sensors are essential in industries such as water treatment, chemical production, food and beverage, pharmaceuticals, and more. Understanding how these sensors work and addressing the engineering challenges they present is key to improving accuracy and reliability.
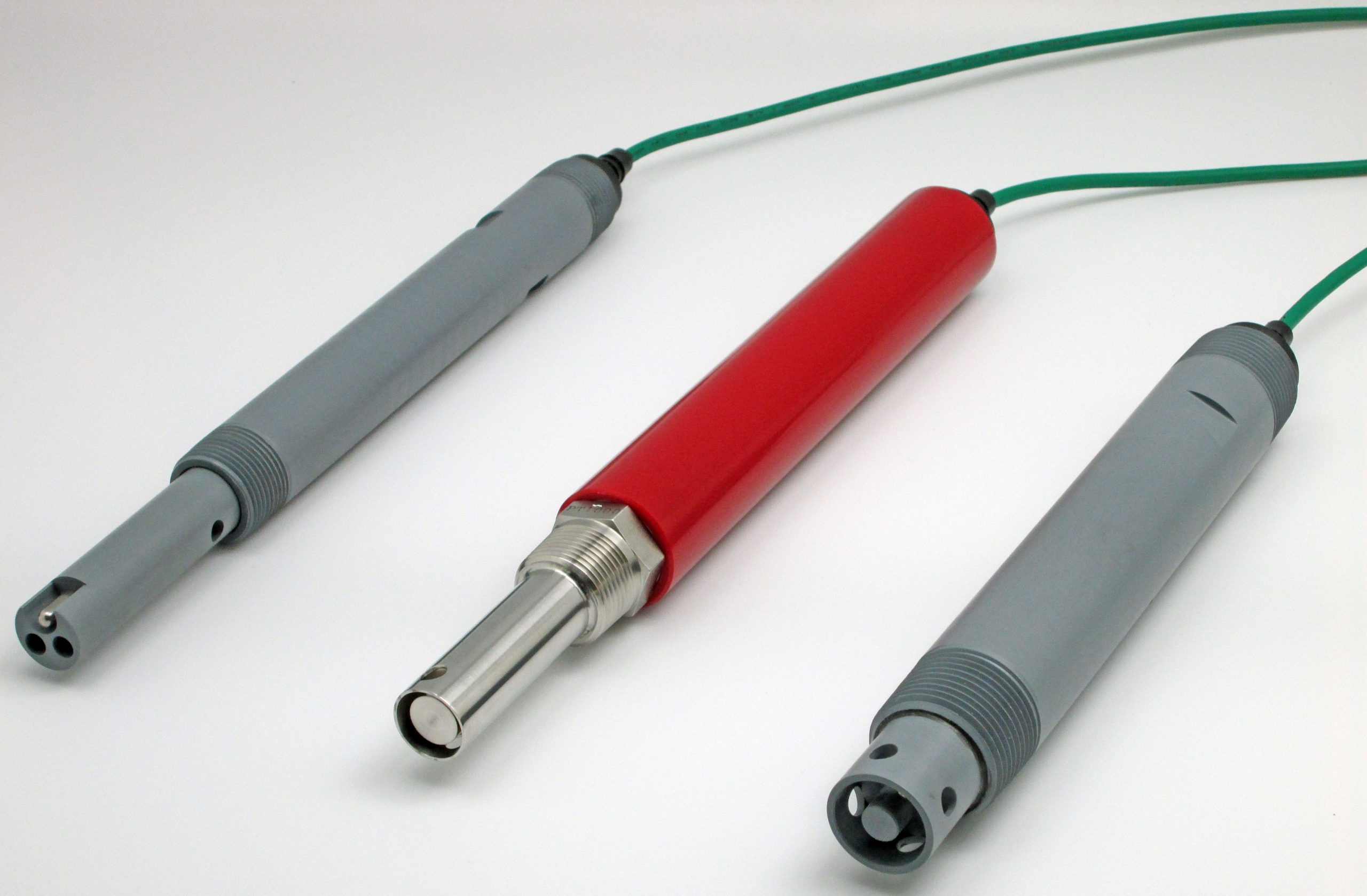
How Conductivity Sensors Work
Conductivity sensors measure the electrical conductivity of a liquid, which is the ability of ions within the solution to carry an electrical current. The basic principle involves applying a small alternating current across two electrodes immersed in the solution. The ions in the liquid move between these electrodes, creating a current that can be measured and converted into a conductivity value.
Two common types of conductivity sensors are contacting conductivity sensors and inductive (toroidal) conductivity sensors. Contacting sensors use direct contact between the electrodes and the solution, making them ideal for low-conductivity applications, such as ultra-pure water systems. Inductive sensors, on the other hand, work without direct contact by using electromagnetic fields, making them more suitable for corrosive or high-conductivity environments.
Engineering Challenges in Conductivity Measurement
While conductivity sensors are effective, several engineering challenges must be addressed to ensure accurate and reliable measurements, particularly in harsh industrial environments.
- Fouling and Contamination: One of the most significant issues is sensor fouling, where residues or particles from the solution build up on the sensor surface, affecting the accuracy of readings. This is especially problematic in industries dealing with wastewater or high-particulate solutions. To address this, ASTI offers specialized sensors designed with self-cleaning mechanisms or materials that resist fouling, prolonging the sensor’s lifespan and reducing maintenance.
- Temperature Compensation: Conductivity is highly temperature-dependent. A change in temperature can significantly impact the ion mobility in a solution, leading to erroneous readings if not properly compensated. Conductivity sensors often include temperature compensation features, either built-in or as part of the control system, to correct measurements for temperature variations. ASTI’s conductivity sensors are equipped with automatic temperature compensation to ensure reliable data even in fluctuating temperature conditions.
- Extreme Environments: Industrial applications often involve extreme temperatures, pressures, or chemically aggressive environments. Designing sensors that can withstand these conditions without sacrificing accuracy is a major engineering challenge. ASTI addresses this by offering rugged sensors built from materials resistant to corrosion and mechanical stress. For example, ASTI’s toroidal conductivity sensors are ideal for measuring in high-corrosion environments due to their non-contact design and durable construction.
- Calibration and Drift: Ensuring the accuracy of conductivity sensors over time requires frequent calibration. Calibration drift can occur due to environmental conditions or sensor aging. To mitigate this, ASTI sensors are designed to minimize drift and feature easy-to-use calibration procedures that maintain accuracy over extended periods.
Improving Accuracy in Conductivity Sensors
ASTI has continually innovated to enhance the accuracy and reliability of its conductivity sensors. One improvement is in the precision of the measurement electronics, which process signals from the sensors. Modern digital conductivity sensors, like those offered by ASTI, provide higher resolution and faster response times compared to traditional analog systems. This not only improves accuracy but also enables more precise control in real-time industrial applications.
Another innovation is the development of sensors that integrate multiple measurement parameters. For example, combining conductivity and temperature sensing within a single unit simplifies installation and improves the overall measurement quality by ensuring that temperature compensation is always accurate.
Conclusion
Conductivity measurement plays a vital role in many industrial processes, but it comes with its own set of engineering challenges. From sensor fouling and temperature dependency to durability in extreme environments, each challenge requires innovative solutions. ASTI’s conductivity sensors are designed to meet these challenges head-on, offering robust, accurate, and reliable performance across a wide range of industrial applications. By focusing on continuous improvements in sensor design and accuracy, ASTI ensures that industrial processes remain efficient, safe, and compliant with the highest standards.